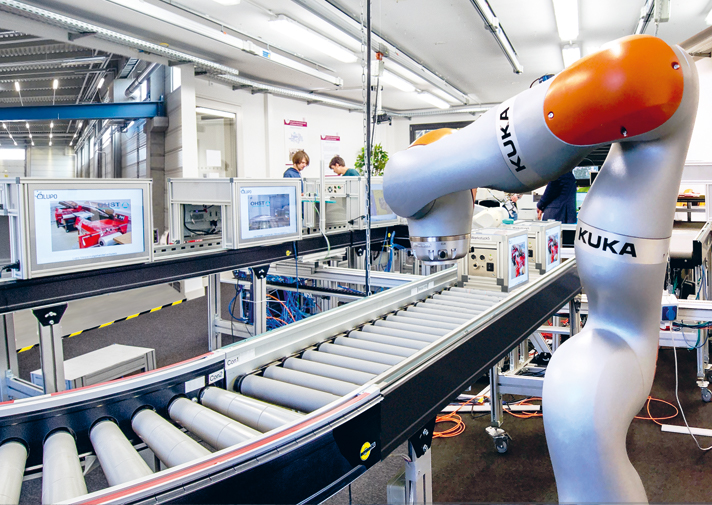
The ironies of automation
01/14/2021Digital assistance systems are intended to instruct people to operate production facilities in industrial production, even without prior knowledge. In an interdisciplinary project, Research Group 1, “Working in Highly Automated, Digital-Hybrid Processes”, and Research Group 7, “Education and Advanced Training in the Digital Society”, are investigating how well step-by-step instruction delivered exclusively by assistance systems works – and where comprehensive training and personal guidance is needed to convey contextual knowledge.
The current phase of economic digitalisation is characterised by an increased use of autonomous technological systems in many areas. Well-known examples of this are navigation systems in cars or autopilot in aeroplanes. Almost the entire process of take-off, flight and landing is controlled by automatic systems, with pilots and air traffic controllers being responsible for monitoring, correcting errors and intervening in the event of technical failure. Yet, since the pilots can rely on the systems in their daily working lives, it is very difficult for them to mobilise the necessary problem-solving knowledge in the event of a sudden technical failure. The recent crashes of Boeing 737 aircraft in Indonesia and Ethiopia illustrate this problem: in these cases, faulty sensor messages prompted incorrect responses by the autopilot, which in turn led to incorrect responses by the human pilots.
In an interdisciplinary project, Martin Krzywdzinski, Norbert Gronau, Gergana Vladova and Philip Wotschak (from top left to bottom right) are investigating how well step-by-step instruction works exclusively via an assistance system.
As autonomous technology becomes more complex, its precise functioning becomes increasingly difficult for employees in the fields of operations, maintenance and troubleshooting to understand. This general problem of autonomous systems is known in research as the “ironies of automation”. The need for knowledge and understanding of complex and abstract processes increases while the possibility for direct feedback and learning decreases. In the current discussion on digitalisation, many have looked to the technology itself to provide the solution: “smart” assistance systems are expected to guide employees in solving the problem. In our research project, we want to question this purely technical approach.
Our research project looks at the knowledge and training that employees need when working with highly automated systems and considers how learning processes and work organisation can be designed to successfully impart this knowledge. In order to investigate this, sociologists, business information scientists and industrial psychologists are working together in the project on an interdisciplinary basis. Sociology usually emphasises the importance of investigating work processes in their specific operational context and uses case studies to look at instances of automation, successful, failing or failed. However, in concrete terms, the research project follows the approach of simulating industrial processes in the laboratory under production-like conditions, which is a procedure from business informatics.
For this purpose, we use the Industry 4.0 Center (FAZI) at the Chair of Business Informatics Processes and Systems at the University of Potsdam, with which the Weizenbaum Institute maintains a partnership. FAZI offers a flexible environment that allows researchers to simulate both “rigid” forms of automation controlled by human labour and highly autonomous (“smart”) forms of automation in which machines interact with each other.
To date, far-reaching insights into how the contexts central to social science research (such as team structures, work organisation, task design and interaction processes) can be operationalised in experimental research designs have not been gathered – either in the sociology of work or in business informatics. This means that new ways of experimental design, operationalisation and measurement must be tested
Our project is designed in two stages. In the first step, we have jointly developed an experiment that deals with the use of digital assistance systems in simple tasks (machine operation). The experiment assumes a highly automated work process in which human workers are responsible for operating the machines (setting parameters, starting work programs) and equipping and monitoring the machines. In this process, they are guided by assistance systems that, similar to a navigation system in a car, tell the workers exactly what they have to do. In the first experiment, one group worked alone under the guidance of the assistance system, while the other group received an additional introduction to the entire work process. The aim was to test how important it is to have a good knowledge of the entire work process, for example, when there are uncertainties and ambiguities in the execution of the work. The working methods and productivity of the test persons in the two scenarios were also examined.
Initial findings from this experiment show that the test persons, who, in addition to being guided by the assistance system, also received a personal introduction to the entire work process, initially made more mistakes when performing the work but achieved a lower number of errors in the final phase. If applied to real employees, this indicates that holistic process knowledge, even in simple machine work, definitely has an added value for companies. This would be a clear argument for investing in skills and training and a clear indication of the limitations of assistance systems.
In this experiment, employees from both groups perceive the assistance systems as helpful – i.e. the group that received an introduction to the overall process and the group that did not receive such an introduction. At the same time, however, many employees in both groups want human support and assistance. This also points to the limits of digital assistance systems and the need to ensure functioning team communication in work processes.
The results provide initial indications that digital assistance systems alone are not enough to overcome the “ironies of automation”. For the next steps, we plan to broaden out the question to include social context factors and to investigate the connection between the autonomy of technology and the design of work organisation. In the sociology of work, case studies have shown that problem solving in complex automated systems requires a collective problem-solving process in which the knowledge of various actors is mobilised to identify the causes of the disruption and to find appropriate responses. Accordingly, we expect attempts to deal with highly automated production processes to not only require process knowledge but also a form of work organisation that offers employees opportunities and support for engaging in discussion and self-organised communication about problems and problem-solving methods.